Celadon Pottery Master Shares Korean Culture in Clay
Celadon pottery is one of the hallmarks of Korean traditional arts. The treasured ceramic is best known for its appealing jade blue surface and unique inlay technique.
Celadon is to Korea what Sevres is to France, Ming to China and Delft to the Netherlands, said Maren Rudolph of the Los Angeles Times. Watch this video as we learn about celadon making from master potter Junghong Kim.
(VIDEO TRANSCRIPT )
The ancient Silk Road had an abundance of goods and ideas transported or traded within.
The cities and towns close to the routes became the emerging global economy. Ancient Korea utilized the over land and maritime routes for great commercial exchanges.
Korean artisans created an assortment of goods and even built structures in Japan. Documented purchase orders during the Silla Kingdom period were of many products but one of great note was the ceramics.
On our Silk Road exploration we spoke with Vancouver-based pottery master Junghong Kim originally from Korea. Celadon pottery master Kim spoke on why Korean celadon is highly regarded.

Master Kim specializes in fingerprint printing style ceramics with fish designs. His beautiful ceramic works (except celadon wares) have been featured in exhibitions in Korea, Japan, Russia and the United States. His never-before-seen celadon wares are currently on exhibit at the Museum of Vancouver until January 6, 2019. (Nikao Media)
Master Kim’s works are currently on exhibit at the Museum of Vancouver. His pursuit for ceramic craft began over twenty-five years ago while still living in Korea.
Master Kim apprenticed with a Korean Celadon Master for seven years. He continued mastering his celadon techniques after coming to Canada.
He wanted to showcase Korean culture through his art. Master Kim is now sharing skills with his many students, and also through his exhibits.
Related: South Korea National Day Celebration Opens with In/Flux: Art of Korean Diaspora
Green Ware that Resembles Jade
Celadon also known as green ware are highly regarded as some of the finest and most sought ceramics by collectors. It’s colour resembles jade, a representation of status, purity and health.
Koreans learned celadon making from China and later exported it to Japan. Korean celadon production started during the Goryeo Dynasty .
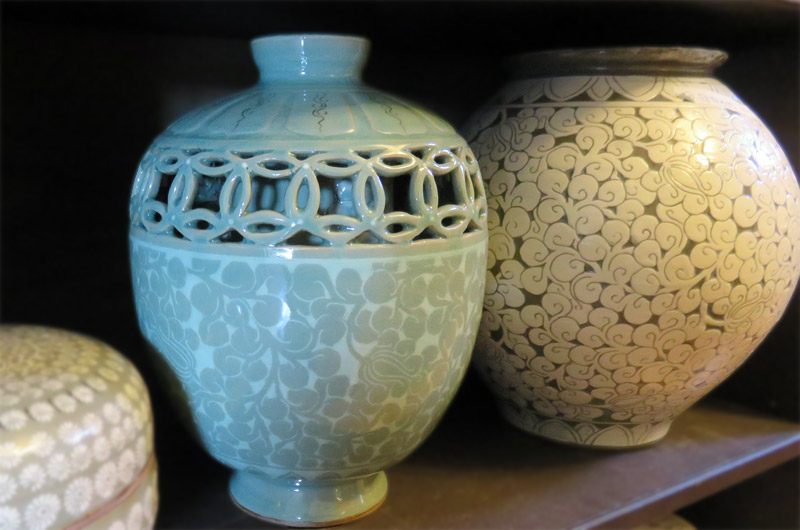
Multi-coloured ceramic designs are created using different types of clay. Master Kim says he uses clay from Korea because it’s dark in colour. Clay from Calgary or USA is lighter in colour. His wife is a sculptor and also assists him in his creative work. (Nikao Media)
Its desirable jade like color and transparent crackle glaze finish are created by the addition of iron oxide into the glaze or onto the clay body itself.
Eleven hundred years ago artisans invented a ceramic inlaid design technique known as Sanggam. Potters would engrave the semi-dried pottery with designs and inlay the engravings with black or white clay.
Dark-colored clay brings out the best results for blue colour on pieces. Master Kim specialty is finger drawn style ceramics.
He believes that earthenware glazed at high temperatures is good for health not the mass-produced wares coated with chemicals and glazed at lower temperatures.
After the first firing a second glazing is applied then fired again. Master Kim strives for perfection. Here he is destroying an imperfect one. It is not uncommon that one out of 500 would be acceptable.